RoBétArmé
Autonomous robotic concrete projection.
![]() ![]() |
Funded by the European Union. Views and opinions expressed are however those of the author(s) only and do not necessarily reflect those of the European Union or HADEA. Neither the European Union nor the granting authority can be held responsible for them.
|
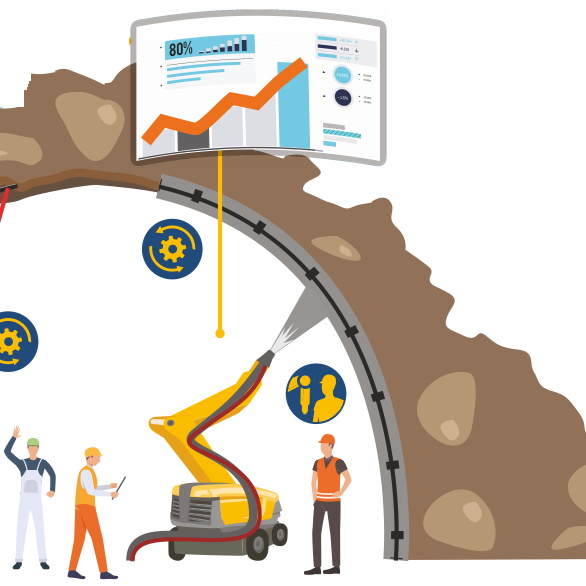
Autonomous robotic concrete projection.
![]() ![]() |
Funded by the European Union. Views and opinions expressed are however those of the author(s) only and do not necessarily reflect those of the European Union or HADEA. Neither the European Union nor the granting authority can be held responsible for them.
|
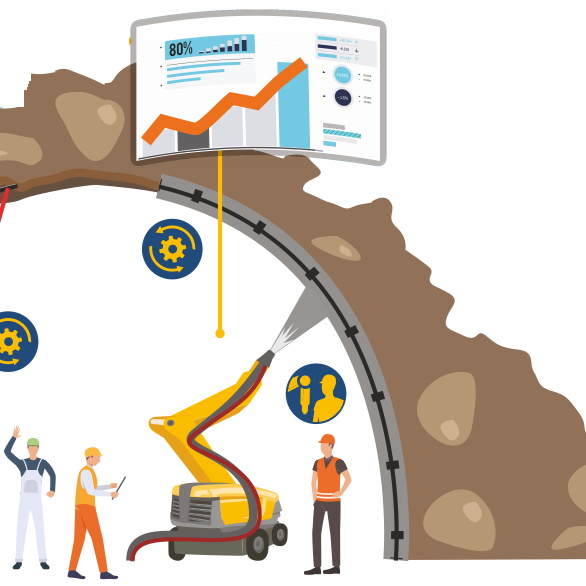
The RoBétArmé project is set to transform the construction industry by automating tough, labor-intensive tasks in shotcrete application, which involves spraying concrete onto surfaces like walls and tunnels. This process is critical for both constructing new structures and repairing old ones. KU Leuven is contributing planning and control methods for both the shotcrete application and the precision finishing of concrete surfaces, including tasks like smoothing and leveling. Backed by the European Commission’s Horizon program, this 42-month project aims to make shotcreting faster, greener, and more efficient, driving innovation in the Construction 4.0 era.
Shotcrete Planning and Control
We develop planning and control systems for shotcrete application in harsh environments, where visibility is severely impaired by dust and occlusions [1]. Our team is working on guiding the trajectory of the shotcrete nozzle using data-driven approaches that can handle noisy and incomplete observations from cameras. By leveraging techniques like deep reinforcement learning and uncertainty-aware algorithms, we enhance the precision of the robot’s movements, ensuring accurate concrete spraying even in difficult conditions.
A key aspect of our work is managing the uncertainty that arises from these noisy inputs. We use machine learning models, such as variational inference combined with reinforcement learning, to estimate the most likely state of the environment despite missing or unclear data. This allows us to make more informed decisions about how to apply the shotcrete efficiently, improving material conservation and reducing waste. Our goal is to create a robust, adaptive system that can handle the unpredictable nature of construction sites while maintaining high-quality outcomes for both new construction and repair projects.
RA-L Publication: AREPO – Uncertainty-Aware Robot Ensemble Learning Under Extreme Partial Observability
In our first journal publication [2] , we ask ourselves how can robots learn effectively in the real world when their vision is noisy, occluded, or incomplete? Our solution introduces AREPO, a reinforcement learning method that quantifies and adapts to uncertainty—unlocking robust decision-making in visually-challenging environments!
✅ Denoised latent representations: We train a VAE to learn, from noisy image inputs, a denoised (latent) representation of the system and a clear and reliable reconstruction of its state.
✅ Uncertainty estimation via Monte Carlo sampling: We quantify epistemic uncertainty by propagating latent variance through the decoder, enabling more informed decision-making.
✅ Uncertainty-guided RL exploration: The estimated uncertainty dynamically modulates maximum entropy RL, prioritizing actions that reduce epistemic uncertainty while improving sample efficiency.
🔬 Results: AREPO achieves state-of-the-art generalization in a high-occlusion industrial task, significantly outperforming standard domain randomization, ensemble RL, and model-based planners in zero-shot sim-to-real transfer.
Robot Manipulation of Amorphous Materials
We are also developing techniques for smoothing and finishing concrete surfaces after the shotcrete process is completed [3]. Using a robot arm, our system automates the delicate task of leveling and refining the concrete surface to meet the required smoothness. This includes developing a visual smoothness estimator, which helps the robot assess the surface condition in real-time and adjust its actions accordingly. The robot can adapt its movements based on this feedback, ensuring consistent and high-quality surface finishes, even in challenging environments where human intervention may be limited.
Our approach involves a layered control architecture [3], [4] that integrates perception, control, and task knowledge. By utilizing a combination of skills for surface smoothing, the robot system can execute specific actions like flattening uneven areas or fine-tuning the surface texture. This architecture allows the robot to adapt to the unpredictable nature of concrete as it settles, improving the overall efficiency and precision of the finishing process. Our contribution helps streamline the final stages of shotcrete application, enhancing both the quality and speed of construction work. We demonstrated this work on a lab testbed for sand profile grading. The adaptive and iterative capabilities of the robot allow it to approach the desired profile with simple control rules that are effective despite limited knowledge of material behavior.
References
-
Benelux[3]Skill-based Layered Control Architecture for the Robotic Manipulation of Amorphous Materials.In 43rd Benelux Meeting on Systems and Control, 2024.